AUTOMATION SYSTEM:
Introducing the AutoRack
Meet the AutoRack from Intec Automation:
The Automatic and Modular Load and Unload Systems Built for High-Density, High-Efficiency Production Environments
Free up valuable floor space, extend operator walkaway time, and streamline multi-step manufacturing with a mobile loading and unloading platform designed for real-world flexibility.
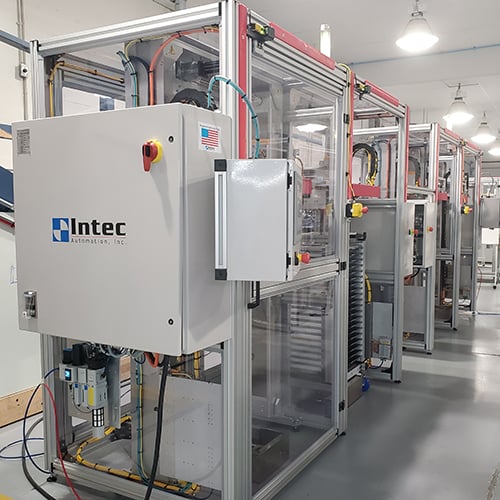
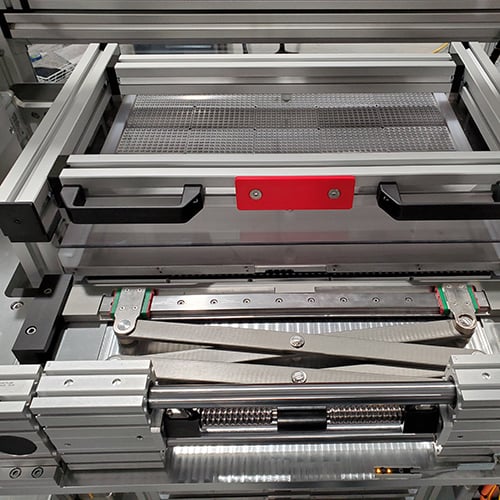
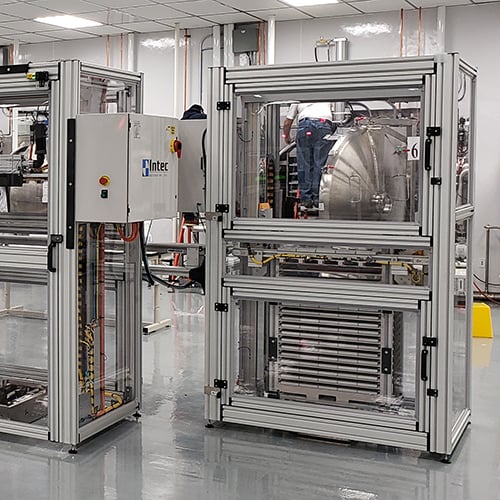
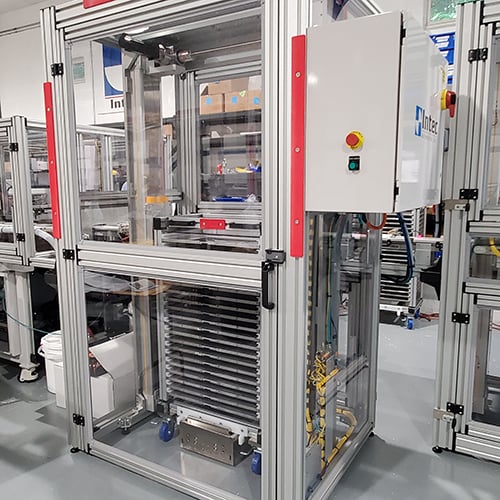
Why Traditional Material Handling Falls Short
Traditional material-handling methods, such as vibratory bowl feeders, accumulation conveyors, magazine stackers, and manual loading stations – often can damage components and introduce more issues than they solve in fast-paced, high-volume production environments. Some of them could be bulky and consume large amounts of floor space, they could demand constant operator attention, and they can create bottlenecks when shifting between different manufacturing steps.
AutoRack solves this with a straightforward and more innovative alternative. Static handling systems are replaced with a mobile, high-density cart-and-nest platform that can be integrated directly into any pre-existing manual, semi-automated, or fully automated station.
The AutoRack does not need to be watched or manually tended to. It handles large volumes of components, giving operators the flexibility to scale output without buying additional square footage.
How the AutoRack Works
The idea behind the AutoRack system is simple: controlled flexibility. Each unit is built around a removable and mobile cart that can be outfitted with a customizable well plate, or, as we like to call it, a nest (a machined plate designed to securely hold products in place during transport and processing) system. These nests can be tailored to fit everything from individual PCR tubes and other diagnostic testing vials to small medical assemblies or electronic components.
For loading, the cart is docked at its station, and, once it is engaged, the system will lift and align the cart to position the shelves. From there, the nests are pushed off of the cart and moved onto cross-conveyors or directly into downstream equipment.
For unloading, the AutoRack goes through the same docking process, but the system receives full nests from the production process and then loads them onto the cart.
Key Benefits
The AutoRack provides a smarter approach to handling complexity in high-mix, high-throughput environments. Designed with flexibility in mind, the AutoRack has many benefits without sacrificing efficiency, including:
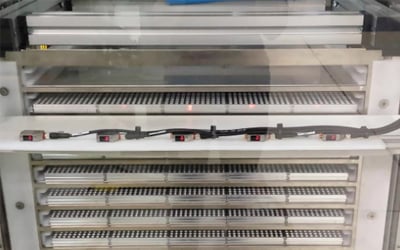
High-Density Storage in Limited Space
Each AutoRack cart can hold up to 600 nests, which dramatically increases the number of parts that can be staged and processed without needing human intervention. Hours of production are condensed into one compact, mobile cart.
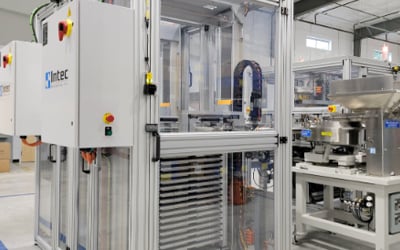
Protects Delicate Parts
The Autorack is ideal for automatically feeding or unloading delicate parts without scratching or damaging them.
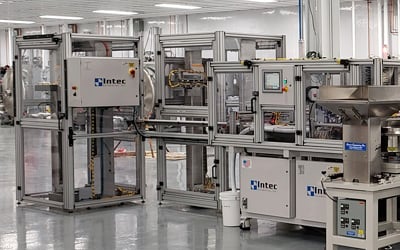
Modular, Customizable Design
From cart height to shelf spacing to nest layout, the AutoRacker is built to be flexible and customized; the units are designed to be scalable across product lines and process types.
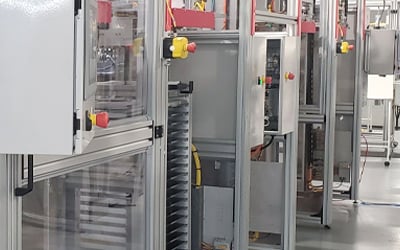
Integration at Any Step
Whether an operation is fully automatic or still manually fed, the AutoRack can adapt and integrate into any existing workflow.
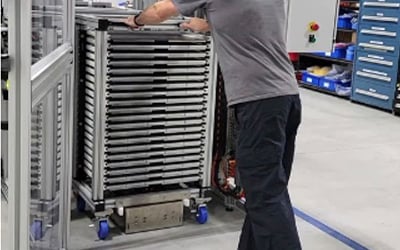
Mobility Across Production
The AutoRack carts are built to be moved by humans but are also AMR-compatible, making it easy to shift products between rooms, process steps, or even temperature-controlled environments like cold rooms.
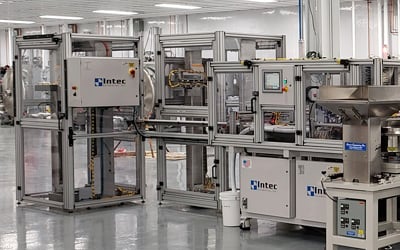
Modular, Customizable Design
From cart height to shelf spacing to nest layout, the AutoRacker is built to be flexible and customized; the units are designed to be scalable across product lines and process types.
Built for Multiple Industries
- Life Sciences and Diagnostics
- Medical Devices
- Light Assembly
- Lab Automation
- Electronics/Semiconductors
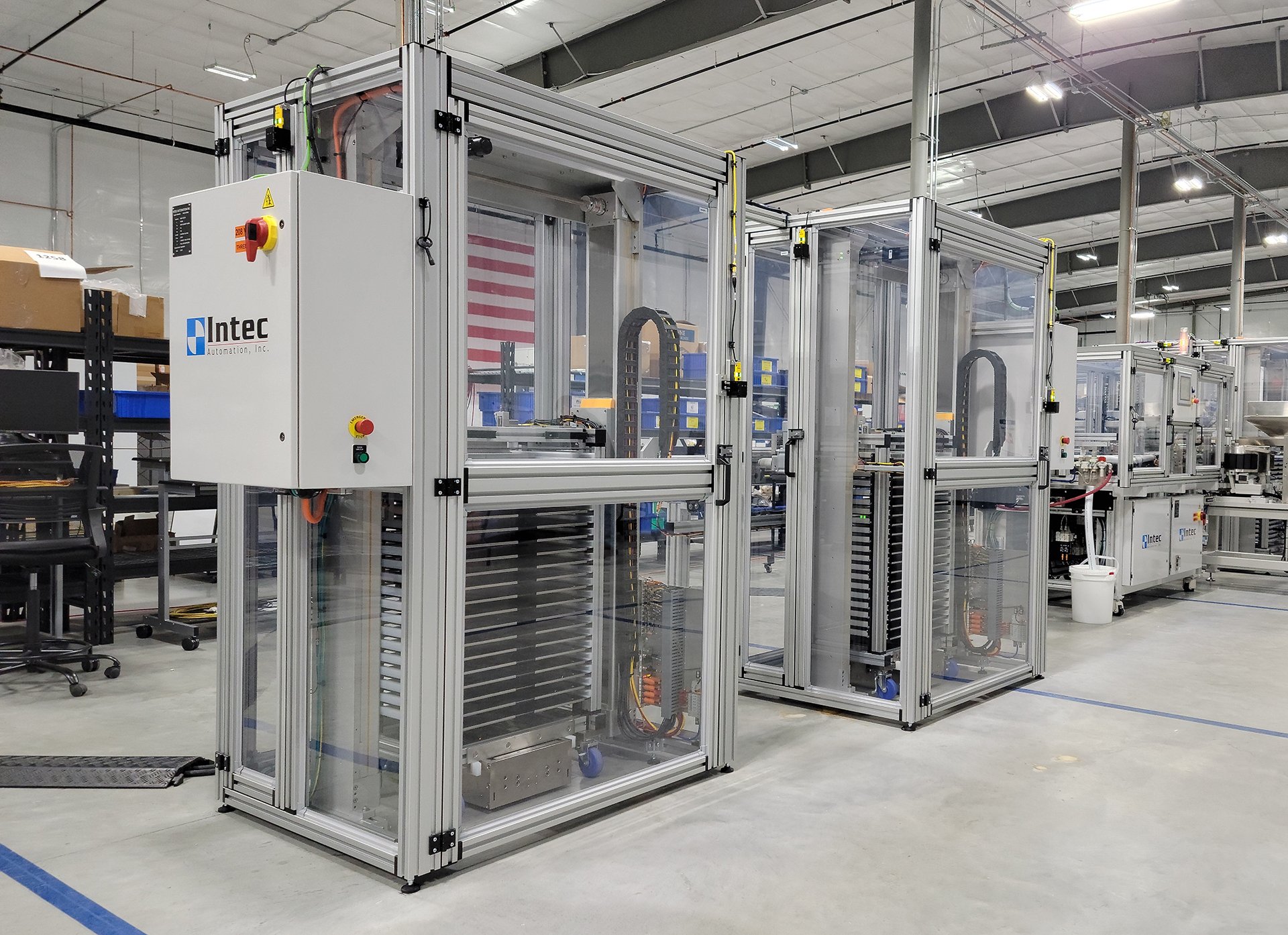
Ready to Integrate
Still relying on stacked trays, operator tending, or conveyors that eat up precious floor space? The AutoRack from Intec Automation is here to replace it all, giving you more control, more capacity, and less effort.
One unit. Three hours of production. No interruptions.
The AutoRack isn’t just a dream. It’s already out and on production lines, saving teams time and labor. It’s also the efficient link between making and meeting a production goal.
Are you ready to up your efficiency? You don’t even need to rebuild your process. You just need the piece that makes it smarter.
Contact Intec Automation and talk to one of our representatives about implementing the AutoRack in your production lines today!
CUSTOM CARTS
Smart Design for Cleanroom and Production Flexibility
- Custom Configuration: Choose left- or right-hand orientation, shelf count, and tray capacity.
- Vision-Ready: Includes flags and grooves for integrated machine vision detection.
- RFID Compatible: Optional RFID tags enable product identification and traceability.
- Cleanroom Friendly: Stainless steel, wipe-down surfaces with sealable grooves.
- Ergonomic & Mobile: Steerable locking casters, lightweight frame, color-coded tray control.
Customize your cart to fit any manufacturing environment.
LOAD MODULE + CART
Automated Tray Handling from Storage to Line
- Integrated RFID and Barcode Scanning: Enables real-time data collection from tray ID.
- Flexible Row Loading: Pushes full tray rows regardless of quantity per shelf.
- Cleanroom Ready: Stainless steel trays, wipeable surfaces, HEPA filtration options.
- Ergonomic Cart Design: Color-coded, steerable, and staging-capable for workflow optimization.
- Failsafe Features: Poke-yoke configuration prevents misaligned tray loading.
- Automation-Ready: Rockwell PLC interface, standalone or integrate with custom systems.
- Optional Customization: Dual-cart setup for uninterrupted load cycles and extended operator walkaway time.
Efficiently load trays into your production line; no operator needed.
UNLOAD MODULE + CART
Automated Tray Collection with Smart Feedback Systems
- Vision & Sensor Detection: Identifies empty, partially filled, or fully filled trays automatically.
- System Feedback: Communicates real-time status to upstream automation.
- Data Logging: Captures load state for each shelf and tray.
- Cleanroom Friendly: Compatible with HEPA enclosure and downdraft filter to remove particulates.
- Flexible Use: Cart detaches for staging, curing, or secondary operations.
- Optional Customization: Dual-cart option available for continuous runtime.
Capture, verify, and offload product trays without interruption.
LOAD + UNLOAD COMBO MODULE
Bi-Directional Handling for Closed-Loop Processes
- Full-Cycle Tray Transfer: Pushes trays into and out of carts in a single unit.
- All-Directional Operation: Enables hand-off between upstream and downstream processes.
- Automation Handshake: Rockwell PLC-based for integration with Intec or third-party systems.
- Staging-Ready Carts: Use for curing, storage, or just-in-time transfer.
- Designed for Scalability: Ideal for complete cells or paired bench-top stations.
Run a complete tray-handling cycle in one smart unit.