Recent advances in a variety of prophylactic and curative treatments have increased the demand for application specific custom bent or formed needles (or entirely unique geometries of cannulas) used in medical sciences today. The World Health Organization reports that around the world, clinicians perform 16 billion injections and conduct more than 234 million surgeries per year. Ophthalmic institutions in the US perform an estimated 3.7 million cataract extractions.
To meet the current demand, cannula and needle manufacturers can maximize profitability by automating their labor-intensive needle bending and finishing operations. With Intec Automation’s needle-bending equipment solutions, you can reduce downtimes, ensure product quality and increase throughput with proven designs and processes that have the highest Overall Equipment Effectiveness (OEE).
Automated Needle Bending Equipment Solutions
Medical device manufacturers are turning to automation to address a range of issues in the sector. Shrinking margins due to rising inflation and increased labor costs are putting pressure on cannula and needle manufacturers, requiring them to optimize production if they want to maintain their profitability.
Manufacturers who rely on human operators to perform multiple manual steps in the process have limited production capacity. By automating the feeding, singulating, orientating, picking, placing, and inspecting operations, you can speed up cycle times, free up human resources, and still deliver according to your customer’s demanding requirements.
In the automated machine cell, you can run multiple concurrent processes. Each station will perform a specific task before handing off to the next process. Every time the machine cell indexes, all stations index a new batch. By running a variety of processes concurrently, you can speed up cycle times exponentially. The program logic handles any faults at a station by coordinating and optimizing the recovery procedures across all other stations, further minimizing downtime. If a manufacturer is doing all these tasks manually, the only way to increase cycle time is by staffing more operators, buying more bench top equipment, or sourcing the additional volumes from a contract manufacturer.
How Does the Automated Needle Bending Solution Work?
Our solution is a completely integrated design that incorporates all of the needle bending and finishing operations. It can handle a variety of formats and accommodate variations in the raw materials fed into the bulk hopper. Operators only have to periodically load the feeding system while all of the remaining tasks are automated. Once completed, the machine either offloads the finished products into bulk bins, or we can integrate downstream packaging equipment to automate the entire finishing operation.
A rotary motion platform indexes the needles and then station-specific fixtures and actuators orientate them, after removing the stock sheaths. Using an in-process inspection solution, we can measure product-to-product variations from the raw material blanks. This allows us to handle and recover from upstream raw-material product variations on the fly.
Bending geometries can include angle bends, radius bends, compound-angle bends, as well as small but precise tip bending. Due to the tight tolerance requirements of the end-customer, any variation in the temper, diameter, and length of the tubing (along with the plastic-molded luer hub) may require fine adjustments during the bending process. Intec Automation can build in contingencies that address these variations to maintain the quality of the final product.
With differences in tubing length, we can determine the exact length using a vision system and compensate for any changes by putting the bending tooling on a vertical precision actuator. For manufacturers, it’s vital to ensure the final geometry of the bent end achieves the desired angle and length.
What Benefits Does Automated Needle Bending Provide?
Automating these labor-intensive processes not only reduces costs but also increases quality and maximizes throughput. Each station in our solutions processes batches concurrently, allowing you to produce up to 3,600 parts per hour (or more).
Intec Automation has the expertise and ability to customize our systems to fit your specific application and accommodate any special requirements. If you need to increase your production capacity, our solutions will ensure you run at maximum volume with minimal downtime.
Automate Your Needle Bending Operation with A Machine Cell from Intec Automation
Intec Automation’s needle-bending equipment solutions are becoming the standard in the industry for automated forming, tip bending, or crimping of needles. The system can integrate with other automated upstream and/or downstream processes and will run as long as required, never tiring or introducing quality issues into the manufacturing line. We can also assist with calculating the potential ROI by switching from a manual operation to an automated machine cell. You can start the conversation today by reaching out to Intec Automation here.
To find out more, download our eBook that discusses the ROI available from automation upgrades for a complex machine cell.
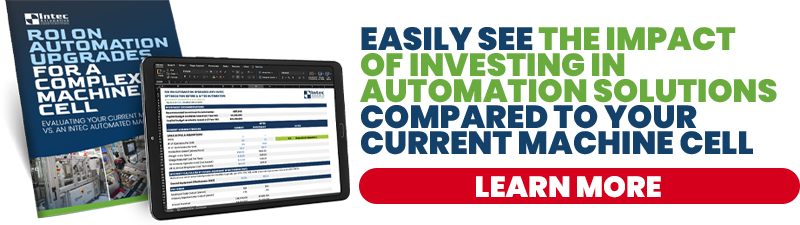